摘要
我們成功開發(fā)出一種快速、非侵入式的在線近紅外(NIR)成像傳感器,用于實時監(jiān)測聚合物薄膜表面的時空結(jié)晶度變化。研究中提出了多元圖像分析和回歸(MIA/MIR)方法,并將其與采用平均光譜或二階導(dǎo)數(shù)結(jié)合 PLS 回歸的標準近紅外校準技術(shù)進行對比。通過各種方法,對高密度聚乙烯(HDPE)、低密度聚乙烯(LDPE)和聚丙烯(PP)聚合物樣品的局部和整體結(jié)晶度變化進行了預(yù)測。結(jié)果顯示,在實驗誤差允許范圍內(nèi),該方法能夠準確預(yù)測由冷卻速率變化所引起的結(jié)晶度微小變化。同時,對結(jié)晶度空間分布的驗證結(jié)果表明,其與加工條件相符。
引言
據(jù) 2005 年統(tǒng)計,全球模塑塑料市場規(guī)模超過 1.56 億噸,其中半結(jié)晶聚合物占據(jù)了相當(dāng)大的比例。僅低密度聚乙烯(LDPE)、高密度聚乙烯(HDPE)和聚丙烯(PP)的消耗量就分別達到 1800 萬噸、2900 萬噸和 4000 萬噸。這些材料的性能對生產(chǎn)條件極為敏感,幾何形狀、壓力和冷卻速率等因素會顯著影響其結(jié)晶度,進而嚴重影響產(chǎn)品的機械、光學(xué)和阻隔性能。因此,在半結(jié)晶聚合物的生產(chǎn)過程中,精確控制結(jié)晶度至關(guān)重要。
然而,從理論上建立加工條件與聚合物最終微觀結(jié)構(gòu)之間的關(guān)系不僅復(fù)雜,而且耗時。目前,塑料薄膜的在線質(zhì)量控制主要集中在形狀、透明度監(jiān)測以及雜質(zhì)、孔洞和劃痕等宏觀缺陷的檢測上。這些方法雖然能夠有效識別宏觀問題,但對于結(jié)晶度變化等細微特征卻難以察覺,導(dǎo)致薄膜成品率通常只能維持在 90% - 95% 之間。
開發(fā)一種快速、非侵入式的在線結(jié)晶度測量工具,對于提升薄聚合物產(chǎn)品的質(zhì)量控制水平具有重要意義。盡管目前測定聚合物結(jié)晶度的方法眾多,但大多數(shù)屬于離線、破壞性測試,且僅能提供單點測量結(jié)果。這些方法通常依賴小樣本量,需要大量的處理時間。例如,最常見的差示掃描量熱法(DSC),通過測量小樣本(通常少于 20 毫克)熔化時的熱量來確定結(jié)晶度,該方法在聚合物分析中應(yīng)用廣泛。此外,原子力顯微鏡(AFM)、掃描電子顯微鏡(SEM)和光學(xué)顯微鏡等多種顯微鏡方法,以及核磁共振(NMR)光譜法,雖能用于聚合物微觀結(jié)構(gòu)表征和獲取相關(guān)信息,但它們存在采集時間長、可能需要表面處理或真空條件,以及成本高、耗時、具有破壞性等缺點。X 射線散射法作為一類非破壞性方法,基于光束撞擊樣品的散射強度提供平均結(jié)構(gòu)和成分信息,但由于其對入射角、散射角、光束偏振和波長的依賴,難以適應(yīng)二維表面掃描。
各種振動光譜技術(shù),如近紅外(NIR),因其快速、非侵入式、幾乎無需樣品制備且能提供大量信息的特點,被提議用于估計聚合物結(jié)晶度。然而,過去發(fā)表的大多數(shù)方法基于單點測量(如使用探針),且通常需為每種待監(jiān)測的聚合物類型建立單獨的校準模型。在高速生產(chǎn)線上,使用這些方法估計較大區(qū)域的結(jié)晶度時,移動樣品或探針操作難度大,而使用探針陣列則會導(dǎo)致表面空間覆蓋粗糙。但精細的空間測量對于識別可能影響材料整體質(zhì)量的局部結(jié)晶度梯度至關(guān)重要,因為局部弱點可能導(dǎo)致整個樣品的機械、光學(xué)和阻隔性能低于規(guī)格,而較粗略的空間分析可能會忽略這些問題。此外,豐富的空間數(shù)據(jù)有助于準確診斷生產(chǎn)線中的操作問題,如聚合物產(chǎn)品的不均勻冷卻。
盡管近紅外光譜已用于分析半結(jié)晶聚合物的結(jié)晶程度和密度,且基于表面反射或吸光度的光譜技術(shù)通常適用于薄膜或薄樣品(小于 2 毫米),因為這類樣品的表面結(jié)晶度在整個樣品厚度范圍內(nèi)具有代表性,但傅里葉變換紅外(FTIR)透射光譜法仍是研究聚合物結(jié)晶度的標準技術(shù),適用于切片機切片、吹塑薄膜或更厚的樣品。紅外反射光譜法也被用于研究聚合物結(jié)晶度,如 Sato 等人在 2003 年收集了放置在旋轉(zhuǎn)槽中的塑料顆粒的漫反射光譜,并使用平均光譜來預(yù)測顆粒結(jié)晶度。此外,還有通過單點激光拉曼光譜法實時估算結(jié)晶度的研究報告。
本研究旨在開發(fā)一種非侵入式的在線傳感器,用于監(jiān)測薄聚合物材料表面的時空結(jié)晶度變化。雖然單點近紅外振動光譜已被證明可用于研究聚合物結(jié)晶度,但本研究重點在于結(jié)合近紅外成像光譜和多元圖像分析與回歸(MIA 和 MIR)方法,以有效獲取樣品的結(jié)晶度空間分布。通過對不同冷卻條件下壓縮成型的薄聚烯烴樣品進行實驗,驗證了所提出方法的有效性。在整個冷卻回路中,非等溫冷卻速率確保了單個樣品內(nèi)的局部結(jié)晶度變化。本研究共比較了四種不同的方法:全平均近紅外光譜或二階光譜導(dǎo)數(shù)與結(jié)晶度測量之間的 PLS 回歸(方法 1 和 2),以及應(yīng)用于近紅外光譜或二階光譜導(dǎo)數(shù)然后進行回歸的 MIA(方法 3 和 4)。將三種聚合物(HDPE、LDPE 和 PP)的結(jié)果整合到一個模型中,而非為每種聚合物構(gòu)建單獨模型,以突顯該方法處理聚合物共混物或復(fù)合材料中復(fù)雜數(shù)據(jù)集的能力。局部結(jié)晶度估計可用于過程監(jiān)控、故障檢測和診斷(如識別不均勻的冷卻速率),或用于預(yù)測薄樣品(<2 毫米)的局部和整體聚合物特性(如機械、光學(xué)、取向等),以實現(xiàn)自動過程和質(zhì)量控制應(yīng)用。當(dāng)然,與任何表面分析方法一樣,該方法在應(yīng)用于較厚樣品時需謹慎。
實驗
材料和工藝
本研究使用的聚合物為商業(yè)聚丙烯(PP)、高密度聚乙烯(HDPE)和低密度聚乙烯(LDPE)。
樣品通過壓機模制成 100 毫米 ×40 毫米 ×1.5 毫米的薄膜。批量處理過程為:在 3 噸壓力、180°C 條件下,將 6 克樹脂模制 10 分鐘,以消除之前的熱歷史。隨后用水冷卻模具,取出樣品。共制備了 18 個樣品,每種聚合物各 6 個,平均冷卻速率分別設(shè)定為 1、2、4、5、8 和 16°C / 分鐘。這些不同的冷卻速率使樣品具有不同的整體結(jié)晶度。同時,水冷回路在每個薄膜內(nèi)引入了樣品內(nèi)部的差異,即每個樣品不僅具有自身的平均結(jié)晶度,其表面還呈現(xiàn)出結(jié)晶度分布模式。
差示掃描量熱法(DSC)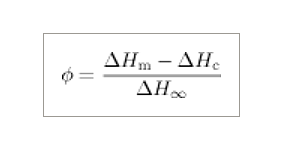
DSC 是一種熱分析技術(shù),用于測量材料的熱流與溫度的關(guān)系。半結(jié)晶聚合物的結(jié)晶度 (?) 可通過熔化引起的吸熱熱流 ( Δ H m )、結(jié)晶引起的放熱熱流 ( Δ H c ) 和 100% 結(jié)晶相的熔化熱 ( Δ H ∞ ) 來確定。
在氮氣環(huán)境下,以 10°C/min 的速率將樣品從 30°C 升溫至 200°C,使用 Perkin Elmer DSC 6 設(shè)備獲得 DSC 熱譜圖。樣品重量約為 7.5 毫克。LDPE、HDPE 和 PP 的熔化峰分別位于 110°C、138°C 和 160°C,溫度范圍分別為 60 - 125°C、90 - 155°C 和 100 - 180°C。100% 結(jié)晶相的熔化熱 (Δ H ∞) 分別為 290 J/g(LDPE)、293 J/g(HDPE)和 207 J/g(PP)。

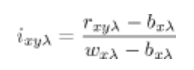
圖像采集
本研究采用的線掃描近紅外成像系統(tǒng)由 Xenic sXEVA - USB - FPA 相機(256×320 像素)和 Specim ImSpector N17E 光柵光譜儀(狹縫:30 µm×14.3 mm)組成,可探測 900 至 1700 nm 之間的波長。樣品上的每條掃描線被 CCD 陣列捕獲為空間 / 光譜圖像(圖 1),該圖像由 256×320 像素組成,空間分辨率為 0.5 mm / 像素,光譜分辨率為 2 nm / 像素。通過將樣品垂直于光譜儀狹縫(沿 y 軸)反復(fù)移動,可獲得整個樣品的高光譜圖像( R )。每個高光譜圖像由 500 個并列的線掃描組成,間隔為 0.25 mm。
線掃描 NIR 成像系統(tǒng)使用鎢鹵素?zé)舻穆涔庾鳛楣庠?。根?jù)方程 (2),利用平面黑色圖像 ( B ) 和純白色圖像 ( W ) 將每個光譜空間圖像 ( R ) 的原始信號轉(zhuǎn)換為反射率單位。平面黑色和純白色圖像分別通過收集保留鏡頭蓋的空間光譜圖像(即暗電流)和對 99% 反射率標準片進行成像獲得。在方程 (2) 中,r xyλ 是原始信號圖像的元素,b xλ 和 w xλ 是黑白校準圖像的元素,i xyλ 是標準化反射圖像 ( I ) 的元素。采用這種簡單的校準方案,成功消除了本研究中收集的 NIR 圖像中遇到的所有線性差異。所有圖像均在受控光照條件下,使用單個成像系統(tǒng)在短時間內(nèi)捕獲。對于長期工業(yè)應(yīng)用,應(yīng)考慮采用更先進的校準技術(shù)。數(shù)據(jù)采集通過 LabView 8.0 界面(National Instruments,德克薩斯州)完成,數(shù)據(jù)分析則使用在 Matlab R14(MathWorks,馬薩諸塞州納蒂克)環(huán)境中開發(fā)的自定義腳本進行。